How Best To Integrate Man And Machine
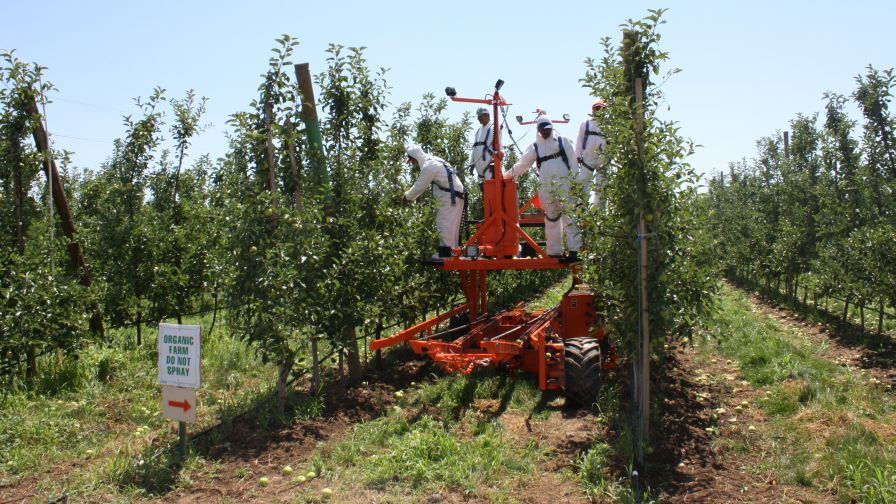
These workers use a platform from Automated Ag for hand thinning. (Photo credit: Christina Herrick)
Karen Lewis, tree fruit regional specialist with Washington State University Extension, often prefaces her talks on mechanization with a tale of two orchards. She drops off two platforms at Orchard A and Orchard B. She goes through how to work the equipment, all the needed how-to information, gets crews started on them, and then lets the crews on each orchard go.
Two weeks later, she returns to both orchards and discovers markedly different attitudes.
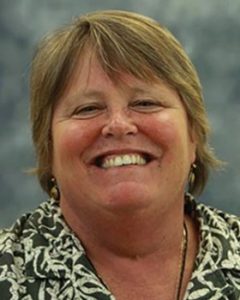
Karen Lewis
“At one orchard [the platforms] haven’t moved, and at the other they won’t give them back to me,” she says.
The difference, Lewis says, is the buy-in from staff and management. At Orchard A, management didn’t have a vested interest in getting workers off of ladders, and so the platform was never seriously considered. At Orchard B, the opposite happened, thanks to management.
“They did everything and anything in their power to make sure to get the right people on the platform, and put them in the right block for the right task,” she says. “Really, it was all about the people, the trees, and the task, and very little about the machine.”
Such is the case with mechanization. A lot of time and energy can be spent on the purchase of labor-assist equipment. But the human element — considering how to best integrate the equipment with your workforce — if often neglected.
Labor is becoming a bigger concern for tree fruit growers throughout the country, and there is a greater focus on labor-assist harvest platforms and equipment. The success of how a piece of equipment will fare hinges upon your staff, experts say.
“If I’m the end user of the product [ i.e. your staff], I’m probably the first person you need to talk to about it,” Lewis says.
Attitudes Matter
Your employees can often feel threatened by a piece of equipment, especially if they feel they will no longer be compensated fairly for performing basic orchard tasks.
Researchers say your workers are more than willing to work harder, i.e. use ladders instead of picking platforms, because they are convinced they will harvest more and make more money at a piece rate.
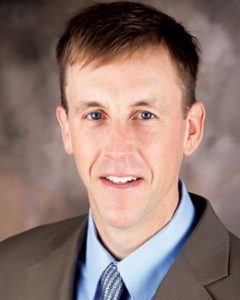
Matt Wells
“Pickers ultimately want to make as much money as possible during the short harvest season,” Matt Wells, production economics and business management specialist with Cornell Cooperative Extension says. “If working on a picking platform will result in less earnings, they would rather pick in the traditional format [even if the work is more strenuous.]”
Man Vs. Machine
For Mark Hermenet of Hermenet Fruit Farm in Williamson, NY, the first experience using a picking platform didn’t go as smoothly as he would have wanted.
“The first day I put one crew on the machine and one crew on the ground. I didn’t think they minded it,” he says. “The guys on the machine seemed to have an easier time and seemed to pick a larger quantity of fruit that day. I told the crew we’re going to do this again and they said, ‘No we’re not.’”
It turns out Hermenet’s crew thought they were able to pick more apples the traditional way because they felt busier.
“It almost feels like you’re not doing much,” he says. “At the end of the day they actually did more on the first day on the machine versus off the machine.”
After that, Hermenet was afraid to bring up the subject of the platform again that first season because he knew he might lose that crew picking for him.
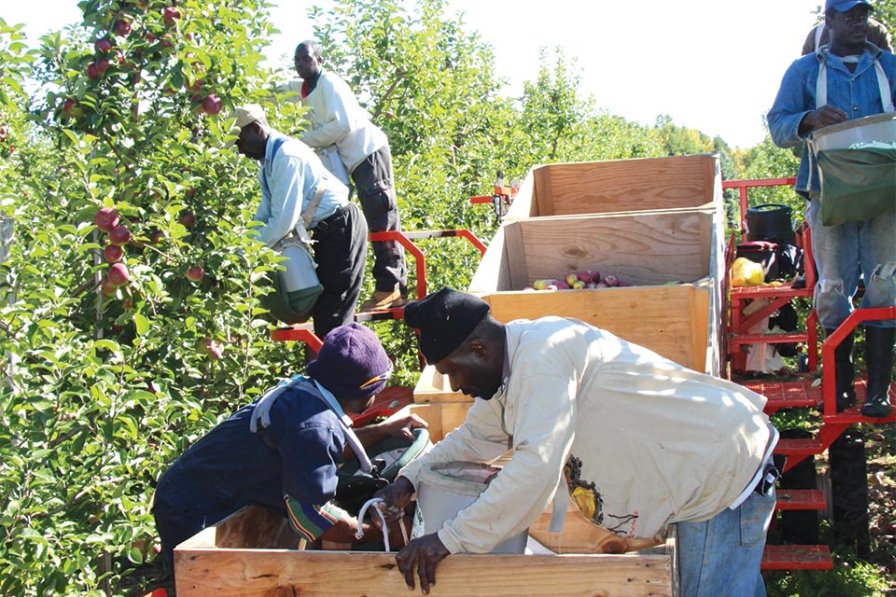
“The guys take it a lot easier if you let them help you, or let them decide themselves what the best balance is, how best to work that machine, within reason,” grower Mark Hermenet says. This team is pictured on an a Huron Fruit Systems picking platform. (Photo credit: Brian Sparks)
Second Time’s The Charm
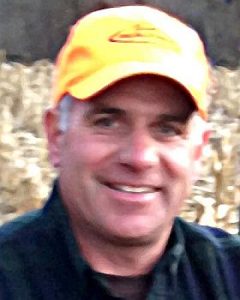
Mark Hermenet
Hermenet opted to use H-2A labor last year, and the results were markedly different. He said the H-2A crew had a vested interest in the success of the orchard, and using the equipment.
“The dedicated employee is one that is going to help you out because they want to come back. In order to come back, you have to be successful or you’re not going to be asked back,” he says.
Hermenet says he gives his crew direction, but also involves them in the solution of how to make it work. Trees in his orchard aren’t perfect in how the fruit is distributed through the canopy, so pickers often need to adjust.
“You have to find the right balance, and the guys take it a lot easier if you let them help you, or let them decide themselves what the best balance is, how best to work that machine, within reason,” he says.
Mario Miranda Sazo, fruit Extension specialist for Cornell Cooperative Extension, Lake Ontario Fruit Program, says it’s the back-and-forth communication which will greatly increase the chance to ensure success.
“It’s not just communication from above on down; it’s a chain of communication,” he says. “Are you having some personal dialogue with your employees? If you’re not doing that today, you are not trying to build your organization.”
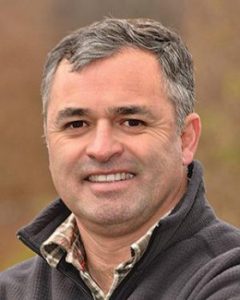
Mario Miranda Sazo
Pay Is Key
To truly improve your crew’s attitude toward harvest platforms, Hermenet says, you have to pay by the hour. He says his crew really enjoys using the platform for thinning, for which they get paid by the hour.
“When using platforms for pruning, hand thinning, and trellising, workers are most often paid an hourly wage. In this case workers will do what is asked of them without complaint,” Wells says. “In the case of harvest, the majority of farms pay by the piece, so a grower has to convince pickers that they will benefit (same or more pay, easier work) using a platform.”
In a time trial at Hermenet’s orchard, he says the results were almost identical in the amount picked on ladders and on a platform, and his crews felt it was easier on the platform.
“At the end of the day they have to make as much money as [they would] picking on the ground or the standard way,” he says. “It’s easier to work on the platform. If we can extrapolate that into the harvest side of it where we can make the same amount of money regardless, and you actually get more work done and they feel better at the end of the day, then they’re going to be on board.”
Miranda Sazo says there are very efficient workers who can pick anywhere from 6 to 11 bins of fruit, without a platform.
“When you bring a machine or a very efficient picking crew from using ladders, you really need to show them with that machine they are going to be even more efficient,” he says.
It’s More Than Just A Relationship
“You need to empower and motivate everyone on that ranch to make that integration successful,” Lewis says. “Involve them or involve their leadership at the beginning.”
Miranda Sazo says an orchard foundation is vital. However, it’s only one piece of the equation.
“A successful grower needs horticulture skills and sound decision-making, but it is beyond that today. Networking, the capacity to listen, to lead the innovation, to build a strong team, these are key.”