Change is Coming to the Fruit Industry: Mechanization is Taking Shape
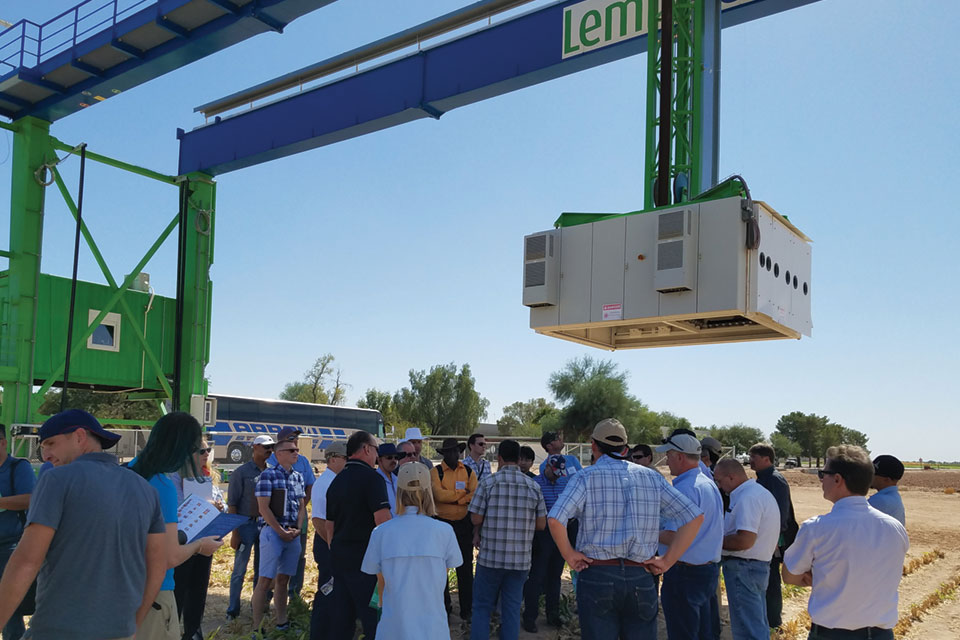
This one-of-a-kind field “scanalyzer” is collecting voluminous amounts of data on a single field in Arizona. Wonder if the fruit growers of 2038 will be able to take such a deep data dive – with their own equipment? (Photo: David Eddy)
When it comes to the mechanization of the fruit industry, and the overall goal of reducing reliance on laborers who will soon become unavailable, we understand your confusion. You want simple answers, but if you get one, be wary.
Sure, mechanization is coming. But when? In what form? No one is exactly sure. Orchard design is a huge factor. So is the level of automation. The makeup of skills on harvest crews has to change, but that’s still a real wild card.
Knowing there is no one answer, we decided to send out a short, informal survey. We asked growers, inventors, researchers, suppliers — anyone with an interest in mechanization in the fruit business — three simple questions.
The response level was outstanding, indicating keen interest, including responses from our two previous Apple Grower of the Year winners, Scott McDougall and Rod Farrow. We know it varies by crop, and because of that, we told respondents this was mainly about apples. Even so, there was still a pretty wide range of answers, indicating little agreement. Many were understandably vague, such as West Mathison, President of Stemilt Growers of Wenatchee, WA, who said they were supposed to test a unit this fall, but it didn’t work out.
“Once we get a good view of the potential of mechanization,” he says, “we’ll have adapted our fruiting structures to better utilize the technology.”
But this we know, unequivocally: Things are going to change. The change may come abruptly, not incrementally. It might be like going from putting a cell phone in your pocket each morning to a model that has a little added feature called a computer. If you want a better picture of what may be coming to an orchard near you, read on. We don’t know about you, but we’re intrigued by this sign from the future: “Hand-Picked Apples.”
When will a commercial mechanical harvester be available to growers nationwide?
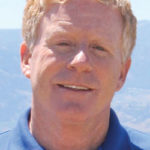
McDougall
With the advancements that have been made in the last several years, I would anticipate that within the next five years that mechanical harvesters should become a reality and be available for growers to use on a commercial basis. — Scott McDougall, Co-Owner, McDougall & Sons, Wenatchee, WA 2016 Apple Grower of the Year
The complication to answering this question is the word “nationwide.” This implies that the same technology will work for everyone, which may not be the case. It appears that some harvester prototypes may be very restricting in the type of canopy they can work in. Some may be somewhat more flexible. I think there will be mechanical harvesters for apples available in the next five to ten years. — James Schupp, Professor of Pomology, Penn State University, Biglerville, PA
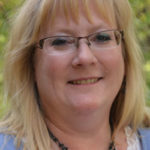
Irish-Brown
Two years ago, I thought I would not see a mechanical apple harvester in my career — it was something 20 years in the future. Then, it seemed like overnight almost, there were three different companies with harvesters in the testing phase with plans for a fully operational machine in two or three years. The challenges in sourcing hand labor have really pushed up the need for a mechanical harvester, so it appears we will have at least one company with a machine ready for growers very soon — maybe in the next 12 months, if not sooner. — Amy Irish-Brown, Extension Educator in Production Tree Fruit, Michigan State University, Grand Rapids, MI
We believe that our robotic harvester will be available to growers by mid-2019. Besides apple, crops will include citrus, peach, pear, pomegranate, mango, and in the future, table grapes. The machine will also thin and prune. — Gad Kober, Co-Founder and Vice President of Business Development, FFRobotics Ltd., Israel
I think we’ll see commercial harvesters available from Abundant Robotics and FF Robotics in two years — so harvest of 2020. — Byron Phillips, National Crop Specialist, Valent USA Corporation, Wenatchee, WA
Abundant Robotics’ goal was to have a commercially ready machine by fall of 2018. I haven’t heard if that’s changed. It is going to take a couple years to set up for and manufacture the machines, so I’m guessing the answer to your question might be 2021-22. — Scott Jacky, Orchard Operations Director, Valley Fruit, Wapato, WA
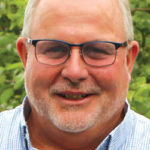
Farrow
I hope there is a commercial robotic prototype working for 2018 harvest, which does not answer your question but does illustrate how quickly a commercial harvester might be available. Realistically we are two to three years away from fully automated harvesters that could pick up to 90% of a crop in a robot-ready canopy. There will be other harvest-assist machines mounted on platforms available sooner that promise increased productivity and reduced fatigue that could be quickly adopted and work in a wider range of canopies but won’t dramatically change the number of pickers. I see a significant risk in machine downtime, especially in the early years. Will you need extra staff capacity or a backup machine waiting in the wings in case a machine is down for a week or longer? We can’t lose much, if any, time during harvest without significant lost revenue. —Rod Farrow, Co-Owner, Lamont Fruit Farm (and) Fish Creek Orchards, Waterport, NY 2017 Apple Grower of the Year
Abundant Robotics should have some equipment available for sale in 2019, 2020. — Tom Auvil, Nurseryman, North American Plants, McMinnville, OR
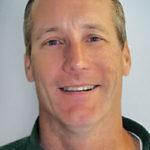
McFerson
In 2018, I expect a limited number of commercial machines will be harvesting apples in Washington, but those machines will be deployed in only a few orchard locations with robot-ready architecture, easily accessible fruit and fully committed growers. Significant commercial rollout in Washington should occur by 2023, but will lag in other apple production areas. —James McFerson, Director, Washington State University Research and Extension Center, Wenatchee, WA
Besides cost, what is the greatest barrier to widespread adoption?
McDougall: The biggest barrier to widespread adoption will most definitely be because of inadequate tree canopy management. Two-dimensional (2-D), planar-type tree structure will be needed to achieve the maximum efficiencies of the harvester.
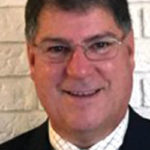
Schupp
Schupp: There are several barriers: A) Orchards with canopy architectures that are compatible with mechanization. It will take time to get the right orchards planted, when we define what exactly is the right system — which is dependent on the actual harvester technology that has yet to be deployed.
B) Shortage of applied scientists and Extension educators to develop/adapt/teach/demonstrate these orchard systems and new technologies. Some say private industry will be able to do these tasks. I do have faith that engineers will develop solutions to the challenges of seeing, reaching, picking and transporting apples to the bins. But to do this, the best experts will still need specialized pomology that the Land Grant schools traditionally supplied. This shortage will become acute as the Baby Boomers retire. Growers may have to become increasingly proactive in working directly with private industry.
C) Capital: The tree fruit industry is already capital intensive; now we will need to re-tool orchards and invest in expensive new equipment even faster than before.
Irish-Brown: The first barrier will be having modern orchard systems in place to use these machines most efficiently — fruiting walls and 2-D orchards will need to replace 3-D systems. The next challenge is the lightning speed that technological innovations occur, and will the first harvesters be the best right from the start, or will there be better machines in the near future?
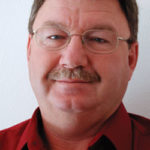
Phillips
Phillips: Orchard systems and topography. While I think mechanical harvesters have a lot of potential on 2-D planting systems, many of our older plantings are still 3-D. Those won’t all get converted overnight, so 3-D orchard canopies will be an initial entry obstacle. Also topography — I’m not sure how stable these are on hillsides so initial use may be restricted to flat ground.
Jacky: In the case of Abundant Robotics, I don’t think the cost of the machine is going to hinder adoption. I believe their business model is going to be like custom harvesting where they come in and pick our fruit at a rate per bin. They know what we pay per bin, and the early numbers they’ve thrown out are a considerable improvement on that. When a machine(s) is developed that will prune, thin, and train in addition to harvest, then the cost of the machine will probably be an issue because it is unlikely that business model will work. The greatest barrier is probably going to be orchard structure. The machine is not going to be effective in orchards that aren’t high density with some sort of tree-training system that allows the fruit to be seen and accessible for it to be picked. To convert to or plant and train an orchard system that will work … that is when costs definitely come into play. Also, with a machine-ready orchard system, there will be a trade-off with production. According to models I’ve worked on, the orchard structure we will need for the machine will not meet the production potential of other systems. Some growers might hold off on using the machine to pick varieties that need the stems clipped if they believe there will be a significant effect on their packouts. Same goes for bruising, but Abundant Robotics has put a lot of effort into keeping that to a minimum. Personally, I’m worried about what happens if a machine breaks down during harvest. There will need to be an IT person nearby as well as a mechanic.
Farrow: Cost, to me, should not be a real factor. Any machine will have to harvest at or very near to the current total cost of using manual labor, or nobody will switch as long as we have a viable guest worker program. The specific skills required to maintain continuous operation of complex hardware and software in the field may well mean robotic harvesting is provided as a contract service in the short term. A bigger issue, especially outside of Washington, will be having a critical mass of suitable orchard canopy across enough varieties to justify having the machinery and skilled labor force available in any small geographic area. I also see a significant risk in machine downtime, especially in the early years. Will you need extra staff capacity or a backup machine waiting in the wings in case a machine is down for a week or longer? We can’t lose much, if any, time during harvest without significant lost revenue.
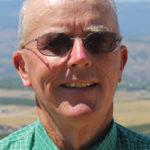
Auvil
Auvil: Canopy maintenance, large branches greater than 3/8 inches, should not be left in the drive row. Anything that limits access to the fruit will limit the amount of fruit harvestable by the machine. Other formats of harvesters may have speed-of-harvest issues. The bin filler is a typical problem. There is only one maker that can handle the volume (18 bins an hour) and large fruit size greater than 250 grams or 72s and larger. The equipment itself can be a barrier to adoption, due to unknowns related to key daily maintenance requirements (such as cleaning or sensor reliability) and availability of service and parts. These machines will need to run 24/7, and downtime will need to be a component of operations management.
McFerson: Orchard configuration and logistics. Regardless of the status of commercially available mechanical harvesters, industry-wide implementation of thin canopy fruiting walls — with all that requires horticulturally — will continue in new plantings and top-worked blocks. However, the relative availability of robot-ready large-acre blocks is a critical barrier to adoption. Equally important will be the capacity of a grower to manage their human workforce, integrate mechanical harvesters into a season-long schedule and minimize downtime due to equipment and/or planning breakdowns.
How advanced will the mechanization of orchards be in 2038?
McDougall: I’m confident that the orchard landscape will be drastically different compared to what we experience today. Just as most growers 20 years ago would have never envisioned the possibility of using robotics as a harvest tool, changes and advancements in technology are occurring at an astonishingly rapid pace! The shortage of people available or willing to work in agriculture, coupled with escalating wage increases and costly government regulatory mandates, will force our industry to find alternative means through mechanization to help reduce our current reliance on a physical labor force.
Schupp: Deciduous orchards will be much more mechanized in 20 years. I think we will see a significant portion of the pruning and harvesting done mechanically, with some hand labor to do certain specialized tasks. I also wouldn’t be surprised to see “hand-picked” or some other appellation for premium, hand-harvested fruit for affluent customers who want to pay a premium. Stranger things have happened.
Irish-Brown: If I look back 20 years and take in all the advances in technology and machines we use today, moving forward 20 years can only bring even more advanced mechanization.
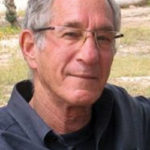
Kober
Kober: By 2038, most fruit harvesting will be done mechanically with advanced robotic technologies, analytics, and cloud services.
Phillips: Highly. Labor has always been our single highest production cost and the least reliable input in terms of availability and skill set. Our newer plantings are being designed with mechanization in mind. Flat ground, long rows, 2-D training systems (we really need to get rid of trellis wires in our 2-D systems next). These planting designs lend themselves well to mechanization of traditionally labor-intensive tasks such as harvest, pruning, and crop load management/thinning.
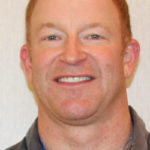
Jacky
Jacky: The orchards have to be fully automated by 2038. That means pruning, thinning, training, and harvest. I believe the biggest challenge we face is going to be surviving the years between when $15 per hour hits and when we are fully mechanized in the orchards … all while relying on labor and capital to develop the orchard structures required for when that day comes.
Farrow: It could (should?) be completely automated long before 2038. Except that any orchard planted in 2018 that doesn’t have a high-enough density to produce large crops on a narrow canopy — 2 feet wide or less — may not fit the systems, yet may well be still in production. There needs to be a rapid shift to fully mechanizable canopies if we are going to get to that goal sooner.
Auvil: Most tasks will be autonomous. Employees will monitor the equipment and sensors to validate the instrument’s decisions. Tractors will be autonomous, irrigation will be scheduled by sensors, and applications will be monitored with flow meters to indicate leaks or lack of application. Fertilizers will be injected into the irrigation. Pruning will be primarily done with hedging, and machines will do the large pruning cuts in the dormant season. Tree training will be done with application of elastic ties by machines (already done on nursery stock in greenhouses). Harvest will done by machine. Pest and disease management will be done with automated traps (already available for codling moth) and sensors.
McFerson: Except for agritainment and niche pick-your-own operations near population centers, orchards in the Pacific Northwest in 20 years will be completely mechanized, but of course will require skilled operators