Investing in New Orchard Equipment Can Lead To a Fruitful Payoff
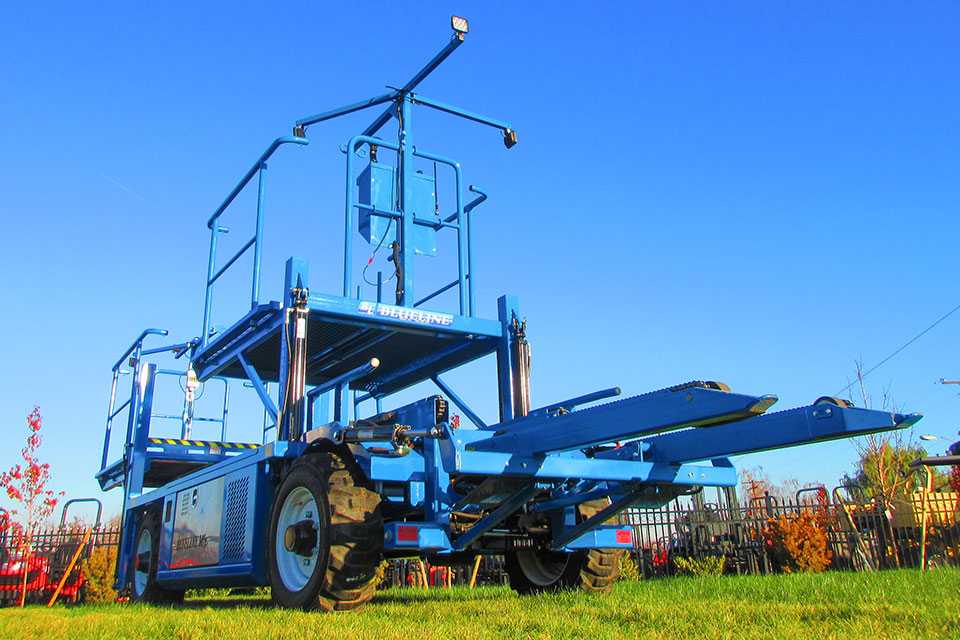
One of Blueline’s latest labor-saving devices, the OPH100N Narrow Orchard Harvesting Platform, has an ultra-sonic auto steering system that eliminates the need for a full-time driver and has zero impact bin drop to maintain top fruit quality.
Photo courtesy of Blueline Manufacturing and Equipment
The most relevant piece of equipment in today’s modern orchard is anything that will increase worker productivity. Those are the words of Gregg Marrs, Managing Owner of Blueline Manufacturing, although most likely every other manufacturer of orchard equipment would echo his sentiment.
Blueline offers five types of self-propelled work platforms, moving workers off of ladders, which “increases worker safety, productivity, and happiness,” Marrs says.
“These machines create improvements in most of the areas (growers) have listed as challenges in the future — worker safety, overtime laws, increased labor costs, and shortages of labor,” Marrs says. “With a proven record of 30% to 50% savings moving from ladders to some form of motorized self-propelled work platforms, growers can solve every one of their challenges. All they have to do is make a few investments in moderation.”
Keep in mind, Marrs adds, that many fruit-growing regions in the world have been dealing with these same challenges for many years and have remained viable by modernizing their orchards and production systems.
Growers should realize the true cost of purchasing new equipment is actually the price less the value of the increase in productivity, Marrs says. For example, a new orchard motorized work platform sells for $80,000, creating payments of about $18,000 per year, but the machine increases productivity about 40%. The annual per-acre labor cost in a typical orchard, not including harvest costs, is about $3,500 for pruning, thinning, tree training, and trellis repair. One-hundred acres multiplied by $3,500 equals $350,000 in labor costs. Forty percent savings equals $140,000 in labor savings. Net improvement to the cash flow winds up being $122,000 per 100 acres,” Marrs says.
“(And) one machine will work effectively on about 100 acres,” he notes. “Growers get confused on what they should be focusing on. It’s not the price of the equipment, it’s the savings the machines produce in their operations.”
POWERED UP
The hand-held electronic tools manufactured by Infaco-USA were born out of a labor shortage, according to Operations Manager Ananda Van Hoorn. “Our mantra has always been that if we can make the work easier, workers can naturally be safer and more productive,” she says.
Van Hoorn repeatedly hears her clients cite two topics: productivity and durability.
“Orchard owners want equipment that has a measurable impact on their productivity, so I see owners investing in platforms and powered pruners,” she says. “A large percentage of orchards are also switching from pneumatic pruning to electric pruning because pneumatics aren’t very durable. They are constantly leaking air and needing replacement parts. On top of that, managing the cables and driving the air compressor, etc., eats into productivity by wasting precious time.”
Growers of high-density orchards who use wires can tie up branches with an electric tie gun and not girdle the branch. This helps tying go three times faster compared to hand tying, Van Hoorn says.
“Additionally, if you’ve got a trellised orchard, you can drive the platform at one set speed because all of the workers can tie at the same speed with a powered tie gun.”
Corona Tools manufactures pruners, shears, loppers, saws, shovels, and rakes. Such power tools can improve the pruning and harvesting process, in some cases, between 50% and 100% while requiring less labor for growers’ needs, according to National Sales Manager Armando Leon.
“The power tools are a bit more expensive but can be justified with the better efficiency and less labor requirement,” Leon says. “The easier the process via automation, the better the profits. And labor is becoming harder to get with stricter immigration laws, requiring the need for more automation and less dependence on manual labor.”
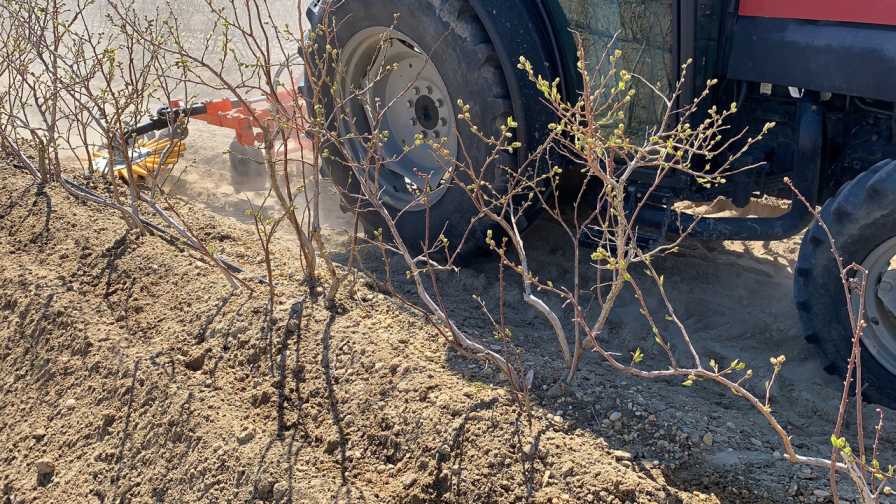
Rinieri’s orchard equipment, distributed in the U.S. by Allen International, can lead to labor savings of 20% to 80%, the company says.
Photo courtesy of Allen International
EQUIPMENT VS. CHEMICAL
As organic farming continues to grow as quick as a weed, the topic of weed control itself becomes more prominent. Not surprisingly, the remedy, according to Allen International, the North American distributor of the Rinieri orchard equipment line, is not chemicals.
“I believe the biggest equipment issue now is weed control,” Rinieri Export Manager and Designer Nicola Rinieri says. “For many years growers have been using the chemical to fight the weeds. In the last three to four years, we have seen a big growth in organic farming. Now farmers want to cut the grass or cultivate the soil, and we do have all the answers to these needs.”
With specialization in blueberry trimming and tilling, Rinieri manufactures more than 70 orchard and vineyard machines. The Bio-Dynamic product line is designed for fast weeding in vineyards and orchards, with a working speed up to 9 mph. The twin-turbo Evo, with electro-hydraulic straddle groups, allows inter-row processing on two rows at the same time.
Labor is also a concern for organic growers, Rinieri says. Mechanical weed control, mechanical trimming, and manual harvesting with a platform will all reduce the need for labor, he says.
“Our equipment can cut the labor down a lot, but it depends always on the starting point of comparison,” Rinieri says. “But it can go from 20% to 80%.”